The Studio
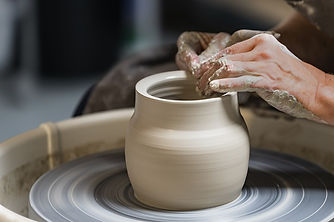
Wheelthrowing
At the very beginning, the wheelthrowing

In the kiln
Then, first firing : the bisque
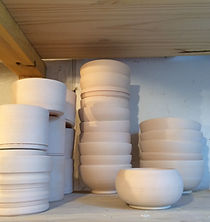
Waiting for glazing
Ready for glazing
There's always something happening at the Studio!
Throwing
In the workshop, there's always something to do. Stoneware or porcelain is first thrown on the potter's wheel and the principle is to prepare the clay.
To make it more 'plastic', more malleable to ensure that all the particles of the material align properly so that, with the centrifugal speed of the wheel, it can be centered and worked on.
Clay is a raw material that has a memory of its shape. Imprecise gestures, errors in throwing, and inevitably these errors will be found in the firing.
This is how you sometimes get an oval bowl! But practice and habit mean that the hands record the right gesture and presto, the bowl is round. One good gesture and the time to raise the piece and a bowl is born in the hands.
In the kiln
Then comes the first firing, which is called the bisque (since the clay is fired twice). This term recalls the vocabulary of pastry making; in ceramics we have common points, I'll even talk about recipes below.
So here are our pieces in the kiln, and off we go for 9 or 10 hours depending on the clay. This is the low temperature (980 degrees C) firing.
We open when the kiln has returned to room temperature, and that's where the last step comes in...
Enameling or Glazing
Once the pieces have been bisque fired, as shown in the third image, it's time to apply the enamel.
The word "glaze" is also used, which evokes the icing of coffee éclairs. And the analogies don't stop there, because this is where the recipe comes in - the enamel recipe, which is composed of different ceramic raw materials and coloring oxides.
The enamel can be applied by dipping, ladling (just like in cooking!), brushing for precise details, or even spraying in an enameling booth.
The Waiting Game
Working with clay is an exercise in patience.
It involves preparing the clay, shaping it, letting it dry for the right amount of time depending on the humidity of the workshop, the season, bisque firing it, waiting for the kiln to cool down before opening to avoid thermal shock that would inevitably break the piece. Lots of steps !
Decorating and enameling also require taking your time and focusing to achieve that final step successfully.
And finally, let it dry again, for as long as it takes, for the humidity to completely dissipate.
Only one step too quick and presto, and the still-damp piece explodes in the kiln, taking its neighbors with it. Catastrophe! Especially if the heating elements are affected!
Pottery is a matter of time that requires taking a step back and concentrating. Resolutely meditative!
Time to see the fruits of our labor!
It's truly the Holy Grail...
Opening the kiln after an enamel firing is like Christmas morning every time. It's an emotion, a frenzy that has had to wait 24 hours before being able to see THE result of weeks of work, patience, and pitfalls.
The success of a ceramic piece is there: when you open the kiln.
Do you know what ? I've often found myself waking up at 4 a.m., going to open the kiln slightly to see if the first shelf at the top of the kiln is successful, if the first pieces are beautiful.
Then... miracle moreoften YES, and sometimes... NO!
Anything can happen in a kiln, the enamel can run, be pitted, have defects, and it's not a good feeling at that moment. But it's a valuable learning experience, to correct one's practice, to do it again, differently.
No matter what, the positive miracle is 80% magical!
Most of the time the pieces are well vitrified, well regular, the enamel is up to my expectations and at that moment I know that they will be on my stand at an exhibition or Christmas market, for sale in my partner's shops, or on the online shop, Ready for love at first sight!
And that's the whole story!
The tour continues to discover my creations, my journey with the origins of the project, the portfolio with my first steps, the blog.
You will read in a few minutes my ceramic travels to Japan and Quebec, a post on art therapy / versus ceramics, another on the birth of a piece or a pottery tool. Click on the relative link to read these blog posts.
And finally to find the online shop to continue the journey.